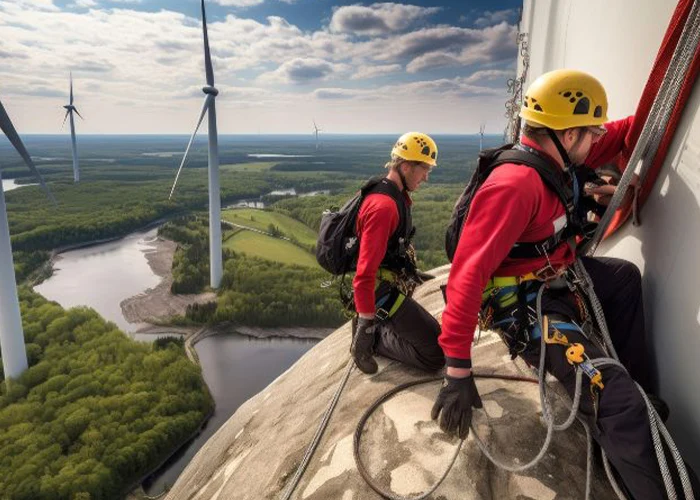
Comment gérer les EPI en entreprise ?
Une bonne gestion des équipements de protection individuelle prévient les accidents et évite les pertes.
Le manque de sécurité sur les chantiers, dans le BTP mais aussi dans d’autres secteurs comme la maintenance d’installations, le levage, les travaux en hauteur, les interventions sur sites sensibles… peut coûter cher aux entreprises en cas d’accident.
Parmi les causes de ces accidents, l’état du matériel et des EPI (Equipements de Protection Individuelle), leur non-conformité ou leur défaut de maintenance en font partie. Le code du travail Art. R 4321-1 précise à ce sujet l’obligation pour les employeurs de « Mettre à disposition des travailleurs les équipements de travail nécessaires, appropriés et adaptés au travail à réaliser en vue de préserver leur santé et leur sécurité ».
Une mauvaise gestion de matériel et de maintenance engage la responsabilité de l’employeur et peut générer des coûts importants pour l’entreprise.
Une solution de traçabilité permet de bien gérer les EPI en entreprise et prévient les accidents.
Notre application de gestion et de traçabilité des EPI permet cela.
TOOLTRACK vous apporte une aide précieuse et indispensable au quotidien pour organiser votre gestion, planifier vos opérations de maintenance et gérer vos stocks.
Quels que soient les EPI à gérer et leur nombre, TOOLTRACK vous aide dans la gestion de votre parc.
Ses fonctionnalités sont importantes pour la sécurité de vos équipes car elles vous aident à prévenir les accidents :
- Suivi de maintenance : planification et enregistrement des opérations de maintenance pour garantir le bon état des équipements, programmation des alertes.
- Contrôles réglementaires des matériels soumis à vérifications périodiques obligatoires : gestion des inspections périodiques pour assurer la conformité des matériels aux normes en vigueur et préserver les certifications, telles que MASE dans le secteur nucléaire, programmation des alertes, gestion et archivage des certificats.
- Réception d’alertes: rappel des échéances de maintenance ou de contrôle pour éviter les risques d’oubli.
- Historique détaillé des contrôles : accès à l’historique complet des interventions sur chaque équipement pour faciliter les rappels de maintenance, la programmation des audits et la prise de décision sur les opérations à réaliser.
- Archivage documentaire : centralisation et mise en sécurité de tous les documents règlementaires nécessaires à produire en cas de contrôle.
Une bonne gestion des EPI vous permet de mettre en sécurité vos équipes et de faire des économies.
Les accidents dus à un matériel défectueux s’accompagnent malheureusement souvent d’un préjudice humain avec répercussions financières qui peuvent être très lourdes à supporter pour les entreprises.
Elles n’ont pas toujours conscience du montant réel du risque encouru qui va bien au-delà du seul aspect matériel.
Sans compter le lourd préjudice moral, celui-ci peut s’évaluer en ajoutant :
- Coûts directs : frais médicaux, indemnisations, salaire versé sur période non couverte par les indemnités, réparations ou remplacement de matériels et d’équipements.
- Coûts indirects : arrêts de travail, embauche ou formation de remplaçants, interruptions de chantiers, pénalités, enquêtes, pertes de productivité, mise en cause du chef d’entreprise ou du chef de chantier et atteinte à la réputation de l’entreprise.
Les petites entreprises peuvent voir leur activité très lourdement impactée et sont particulièrement vulnérables dans ce domaine.
Une bonne gestion des équipements de protection individuelle (EPI) tels que casques, chaussures de sécurité, vêtements de protection, gants, appareils respiratoires, harnais, cordage… est donc un préalable essentiel pour prévenir les accidents.
Elle aide à les maintenir en bon état d’usage, à garantir leur conformité et à assurer la sécurité des équipes.
La traçabilité des EPI aide aussi à assurer leur suivi, à gérer les affectations et à réduire les pertes pour faire des économies.
Quels sont tous les bénéfices d’une bonne gestion des EPI avec notre logiciel TOOLTRACK ?
Quel que soit votre secteur d’activité et vos matériels, notre solution est faite pour vous aider à gérer votre stock d’EPI et à organiser leur maintenance pour protéger vos collaborateurs :
- Prévention des accidents : vous gérez la maintenance de vos EPI et suivez leur statut, vous réduisez significativement les risques liés à l’utilisation de matériel défectueux ou non conforme.
- Réduction des coûts : vous diminuez immédiatement les dépenses induites par les accidents, les arrêts de travail, les interruptions de chantiers, les pertes, le rachat de matériels ou la location…
- Conformité réglementaire : vous planifiez vos contrôles périodiques, vous respectez vos obligations, les normes concernant vos matériels, vous gérez vos certificats de contrôle et assurez votre conformité.
- Optimisation de productivité : vous gérez les affectations de matériels, garantissez à vos équipes la disponibilité de leurs équipements, vous leur permettez de travailler plus efficacement avec du matériel bien entretenu, en toute sécurité, avec davantage de confiance dans leur entreprise.
La traçabilité et le suivi rigoureux du matériel et des EPI (équipements de protection individuelle) sont essentiels pour assurer à la fois la sécurité des équipes et la pérennité de l’activité.
Faire le choix d’une application comme TOOLTRACK vous aide à mettre en place les bonnes pratiques pour prévenir les accidents, réduire les coûts, maximiser la sécurité des équipes et protéger leur activité sur le terrain.
Dans tous les cas, vous serez vite gagnant.
Pour aller plus loin, essayez notre calculateur pour avoir une idée des coûts liés à une mauvaise gestion de matériel et vous verrez que l’utilisation de TOOLTRACK sera très vite rentable.
En quelques clics, vous pourrez simuler les économies que vous réaliseriez grâce à une gestion optimisée de vos EPI et de vos matériels avec TOOLTRACK et son application mobile.