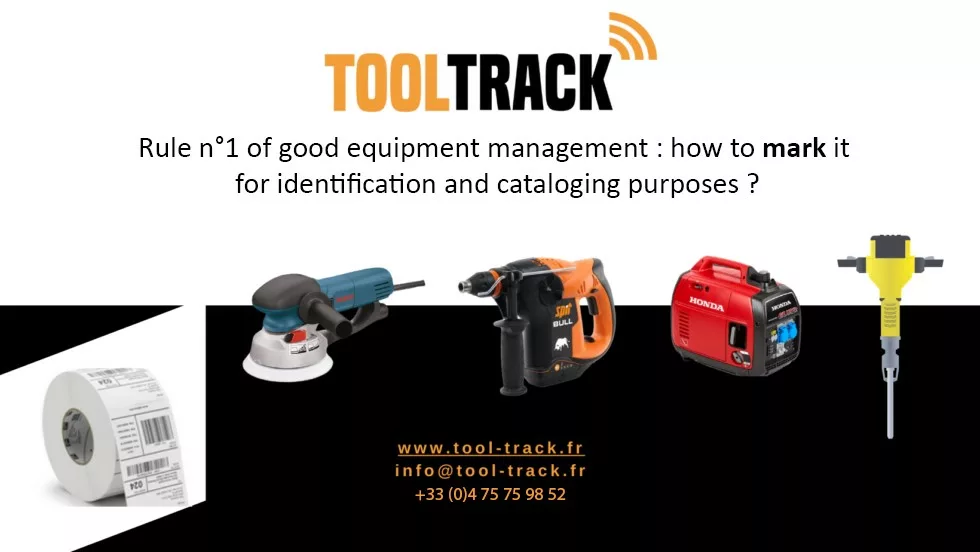
Rule no. 1 of good equipment management: marking
Good equipment management is a recurring concern for companies, but the issue really becomes crucial when problems arise: equipment doesn’t come back, equipment is abused and has to be replaced too frequently, too much breakage, too much time spent looking for equipment that needs maintenance, lost periodic inspection certificates, etc.
TOOLTRACK is a highly effective digital solution that immediately helps you to be much better organised, to manage your equipment with just a few clicks to avoid all these problems, and to be more profitable.
But when it comes to equipment management, there are also rules and good practices to be applied if you want to achieve the best results.
Here we share with you the No. 1 rule of good equipment management, the one you should start with.
The number one rule of good equipment management: marking.
The 1st major question to ask is how to identify and list each item of equipment to be tracked.
Properly marking your equipment means asking the right questions to make the right choices:
- What equipment is involved?
- What material is the base made of?
- what is it used for?
- under what specific conditions is it used?
- what data is expected on the equipment?
- what are the objectives of tracing?
Our advice for appropriate and effective marking of your equipment
– For small items of equipment, power tools, safety equipment and PPE, marking and tracking is generally done using QR-Code or RFID tags. Advantages: you can manage individual assignments, stocks, maintenance and track movements.
– For small vehicles, such as trailers, tippers, generators, mixers, etc., marking is best done using battery-powered trackers or Bluetooth beacons. Advantages: no internet connection. No battery required. Low power consumption.
– For large site machinery such as backhoe loaders, loaders, cranes, excavators or vehicles: marking is done using on-board telematics and geolocation. The advantage: information on position and movements is transmitted in real time.
There is a marking solution for every type of equipment, but it’s important to ask the right questions beforehand to make the right choices, because the economic impact is not the same and oversized investments can be avoided with the right advice.